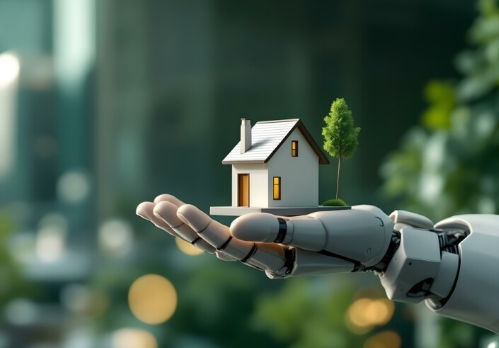
A Canadian company and its team of robots aim to
enter the U.S. market with the promise of saving time, cutting
costs, and addressing labor shortages for high-volume home
builders.
Toronto-based Promise Robotics is targeting several U.S.
markets—including Atlanta, Austin, Charlotte, Chicago, Dallas,
Houston, Nashville, and Phoenix—to set up factories where
AI-powered robots similar to the ones operated by automakers
would produce key home building components, including walls,
stairs, and floors.
Ramtin Attar, the company’s co-founder and CEO, stated that
Promise Robotics will establish a robot-equipped plant ranging
from 50,000 to 60,000 square feet in each U.S. market where it
operates. As a result, no Canadian-made products will be shipped
to the U.S., thereby avoiding any tariffs. Each factory, staffed
by four to six robotic workers along with human employees, will
be able to serve several high-volume builders within
approximately a two-hour travel radius.
Promise Robotics’ technology aims to shake up the currently
“fragmented” home building process. A Promise Robotics factory
can take on about 15% to 30% of the work involved in building a
home, he said, with the rest of the work—like installing kitchen
cabinets, bathroom fixtures, and bedroom carpeting—still being
carried out traditionally.
“We basically tell a home builder that you’re able to double
your capacity, not your overhead, and build 60% faster,” said
Attar.
Promise Robotics reported in October 2023 that it collected $15
million in venture capital, bringing its fundraising total to
$25 million. Investors include Horizons Ventures, Radical
Ventures, Canada’s Public Sector Pension Investment Board, the
United Brotherhood of Carpenters, Relay Ventures, Alate
Partners, and Sustainable Development Technology Canada.
Attar said his company plans to launch U.S. operations in 2026.
Promise Robotics is in talks with several high-volume home
builders in the U.S. about signing up for its “home building
factory-as-a-service” platform. The platform produces a fully
framed and locked-up house with windows, doors, and mechanical,
electrical and plumbing rough-ins.
Builders will be invited to invest in local factories through
profit-sharing deals, Attar said.
The company already operates a factory in Edmonton, Canada, and
just announced it will open a 60,000-square-foot facility this
summer in Calgary, Canada. Promise Robotics says the Calgary
factory will be able to produce as much as 1 million square feet
of housing per year. That pace would equate to 500 traditional
2,000-square-foot homes in a year’s time.
Attar said the robotic manufacturing process can be applied to
conventional homes, townhomes, duplexes, and other types of
housing.
Promise Robotics, founded in 2020, explains that its
robots—driven by the company’s proprietary Big Brain AI
software—interpret builders’ blueprints to create
machine-precision components such as walls, floors, and stairs.
Those components are then assembled at builders’ homesites.
Attar said the company’s tool-outfitted robots focus on
lumber-based construction. However, the company is receiving
requests to incorporate cold-rolled steel for construction of
commercial buildings.
For a typical single-family, two-story home, it can take about
eight hours for four robots to manufacture components (including
floors, walls and stairs) and another six hours to assemble the
components at a homesite, Promise Robotics says. This process
can reduce a builder’s cycle times by 60%, and save roughly $350
per day during a six-week build. So, over that six-week span,
those savings could approach $15,000.
A Promise Robotics factory can also pre-install features such as
HVAC and plumbing systems.
Aside from producing components for new homes, Attar said
Promise Robotics can work directly with a builder’s suppliers to
source various materials, and can even train a builder’s crews
on assembly techniques or provide on-site installation teams.
“As long as you’re bringing demand, you don’t have to worry
about a thing. We have that entire product flow worked out as
one package, but we are happy to work with your existing supply
chain. So, if you already have trades and manufacturers that
you’re working with, we’re happy to chat with them about joint
venturing and partnering.”
Source:
builderonline.com